Lessons from the Field: RIA Members Tackle Complex Losses with Precision
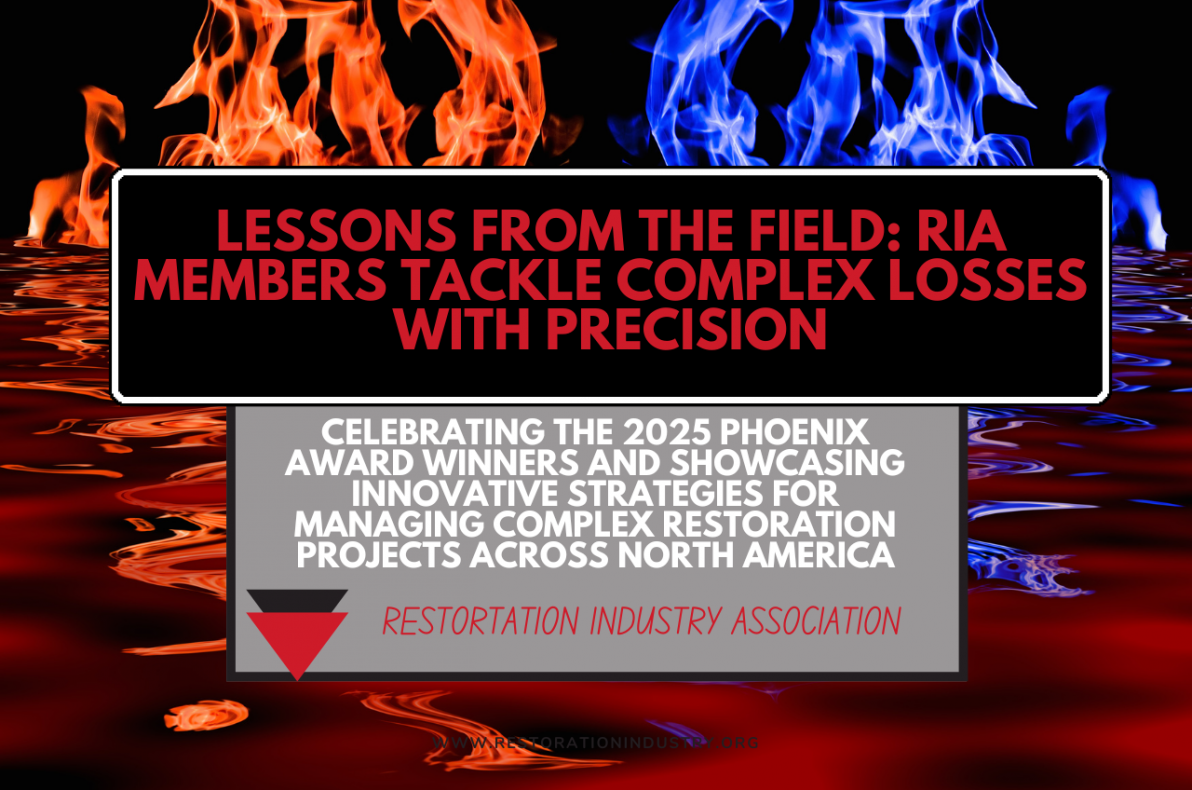
Celebrating the 2025 Phoenix Award Winners and Showcasing Innovative Strategies for Managing Complex Restoration Projects Across North America
In restoration, complex losses test even the most experienced teams, pushing project managers to coordinate multiple moving parts while keeping projects on time and within budget. Whether it’s rebuilding high-rise towers after hurricanes, remediating large-scale fires in manufacturing plants, or navigating environmental challenges following major disasters, RIA members are at the forefront of managing these demanding projects with skill and precision.
This year’s Phoenix Award winners and nominees showcase what’s possible when restoration professionals pair advanced technical expertise with streamlined project management systems. From overcoming supply chain delays to managing multi-vendor teams and ensuring clear documentation every step of the way, these projects highlight how RIA members are solving the toughest challenges while delivering on time and within scope.
Join us as we celebrate the award winners and recognize all submissions, offering a behind-the-scenes look at how RIA members are redefining complex loss management across North America.
About the Phoenix Awards
Established in 1997, the RIA Phoenix Awards honor exemplary achievement in the restoration and reconstruction industry. The awards highlight projects that embody the resilience, excellence, and transformative impact of restoration professionals who help rebuild lives and communities after disaster.
This year’s winners, ATI Restoration, LLC, have been recognized for two extraordinary projects that exemplify the spirit of the Phoenix—rising from disaster to deliver hope, resilience, and renewal.
Winner Phoenix Award for Innovation in Reconstruction
Project: Reserve at Lake Pointe Reconstruction
Location: St. Petersburg, FL
Company: ATI Restoration, LLC
After Hurricane Milton devastated the Reserve at Lake Pointe, displacing hundreds of families and leaving 65 apartment buildings uninhabitable, ATI Restoration mobilized immediately. In just four weeks, the ATI team completed the reconstruction of 250 units across a mile-long complex—an extraordinary feat achieved through advanced logistics, on-site innovation, and a deeply compassionate response.
The transformation of the leasing office into a centralized command center and a triaged scoping process allowed crews to rebuild with speed, quality, and care. Beyond construction, ATI provided critical support to displaced residents, offering meals, helping families transition into temporary housing, and restoring a sense of home. This project redefined the possibilities of disaster recovery by combining innovation with community-centered impact.
Submissions for Phoenix Award for Innovation in Reconstruction
Project: Bayport Plaza Restoration Project
Location: Tampa, Florida
Company: ATI Restoration, LLC
ATI Restoration is proud to present the Bayport Plaza Restoration Project as a nominee for the Phoenix Award for Innovation in Restoration. Following catastrophic damage caused by Hurricanes Helene and Milton, this large-scale restoration effort exemplifies the highest standards of innovation, technical precision, and resilience in the face of crisis.
Bayport Plaza, a Class A high-rise, sustained severe losses including 60% roof destruction and widespread water infiltration across all 11 floors. Tenant areas were flooded, ceilings collapsed, and critical infrastructure failed. ATI responded within 30 minutes of notification, rapidly mobilizing to assess the damage and initiate an effective, large-scale recovery operation.
One of the project’s key innovations was the placement of power generators directly on the roof, which allowed for faster and more efficient power distribution without the need for expensive and time-consuming cable routing. This solution enabled a quicker return to operational status and significantly reduced business interruption costs.
Throughout the project, ATI demonstrated resourcefulness and dedication. Despite the initial lack of elevator access, the team formed a human assembly line to move more than 300 pieces of critical equipment up 11 flights of stairs. Negative air machines, hydroxyl generators, and hospital-grade cleaning—validated by bacterial swab testing—ensured the highest standards of environmental safety and sanitation.
ATI’s meticulous approach also resulted in substantial cost savings: 98% of the building’s interior glass panels were preserved, and a temporary roof solution was engineered to serve as the base for the permanent roof—minimizing waste and maximizing efficiency.
________________________________________________________________________
Winner Phoenix Award for Innovation in Restoration
Project: Fire Restoration in a Food Processing Facility at SunWest Milling
Location: California
Company: ATI Restoration, LLC
Following a catastrophic fire at SunWest Milling—the largest rice mill in California—ATI faced the challenge of restoring over 37,800 sq. ft. across two 170-foot towers and an underground tunnel, all while maintaining full operational capacity.
With a complex, multi-level layout and strict FDA compliance requirements, ATI developed a detailed Critical Path Method (CPM) plan, employed innovative use of conveyor man-lifts and hoist systems, and implemented containment strategies to perform asbestos abatement, fire remediation, and full-scale restoration without halting production. Their work not only restored the facility, but prevented major disruptions to the regional food supply chain. The result: a project completed on time, safely, and with lasting improvements to operational efficiency.
“These projects reflect the highest standards of our profession—where technical mastery meets real-world impact,” said Nicole Sargent, Director of Operations for RIA. “We congratulate ATI Restoration for demonstrating what’s possible when innovation, leadership, and purpose align.”
The Phoenix Awards were presented during RIA’s 2025 International Restoration Convention + Industry Expo in West Palm Beach, FL. Winners received recognition in front of hundreds of industry leaders, along with complimentary registration to the event.
Submissions for the Phoenix Award for Innovation in Restoration
ATI Restoration, LLC
Project: Tustin North Hangar Environmental Remediation
Location: California
When the historic Tustin North Hangar—one of the largest wooden structures in the world—was destroyed by fire in November 2023, asbestos-containing materials (ACM) spread across a six-mile radius, affecting thousands of homes, schools, parks, and public infrastructure. ATI Restoration, LLC mobilized immediately, deploying over 500 certified professionals and certifying an additional 125 asbestos technicians to meet the unprecedented demands.
Working through major holidays, ATI implemented a comprehensive zoning strategy, prioritized high-risk areas, and launched door-to-door community education efforts to ensure transparency and build trust. In total, hazardous materials were removed from over 2,500 structures, and third-party audits confirmed no detectable asbestos fibers above screening levels. ATI’s swift response and strategic approach helped protect public health and restore community confidence—demonstrating leadership, technical mastery, and a deep commitment to service in the face of crisis.
ATI Restoration, LLC
Project: Bayport Plaza Hurricane Restoration
Location: Tampa, Florida
When Hurricanes Helene and Milton struck Tampa, Florida, Bayport Plaza—a Class A high-rise office tower—suffered catastrophic damage, including 60% roof loss and severe water infiltration across all 11 floors. ATI Restoration, LLC responded within 30 minutes of notification, launching a full-scale emergency response that minimized tenant displacement and significantly reduced business interruption.
Innovative solutions included installing power generators on the roof to streamline power distribution and forming a human assembly line to carry over 300 pieces of critical equipment up 11 flights of stairs while elevator access was unavailable. The team preserved 98% of the building’s interior glass panels and used hospital-grade cleaning practices verified by bacterial swab testing. Temporary roofing served as a base for the permanent solution, saving time and cost.
The Bayport Plaza project highlights ATI’s exceptional ability to combine innovation, technical expertise, and cost-efficiency in the face of disaster—restoring not just a building, but business continuity for its tenants.
COIT Restoration
Project: Reno Apartment Complex Fire Recovery
Location: Reno, Nevada
Following a devastating fire caused by an industrial heater, a five-story, 368-unit apartment complex in Reno suffered extensive fire, smoke, and water damage across multiple floors. With 93 units affected and structural damage exposing the building to the elements, the situation demanded swift, strategic, and collaborative action.
COIT Restoration took the lead, forming a coordinated unit-by-unit schedule that guided all project partners, including contractors and hygienists. Daily Field Reports were implemented to document progress, resource usage, and visual updates. Despite the complexity of the job and the presence of multiple teams on-site, COIT restored the 350,000-square-foot property in just 120 days using a 136-person crew.
The result: millions saved in rebuild costs and a model demonstration of project leadership, operational discipline, and restoration excellence.
Paces Restoration
Project: Frye Family Fire Rebuild and Home Transformation
Location: McDonough, Georgia
After a devastating electrical fire destroyed their longtime family home in November 2023, the Frye family turned to Paces Restoration to help them rebuild—not just what was lost, but something even better. Overcoming significant insurance coverage limitations, structural concerns, and permitting challenges, the Paces team, led by Craig Collins, collaborated closely with the family to design and deliver a fully customized, energy-efficient home that exceeded their expectations.
Craig’s 30+ years of construction experience and personal approach to client relationships were instrumental in helping the Fryes navigate this traumatic event. From working with engineers to ensure the slab could be reused, to managing a framing revision mid-project to add a new bonus room, the project was marked by creative problem-solving and an unwavering focus on the client’s needs.
Sustainable upgrades like spray foam insulation and a tankless water heater brought long-term cost savings, while adherence to the insurance draw schedule and ALE limits ensured the family could return home on time. Today, the Fryes remain in close contact with Craig, grateful for the professionalism, care, and craftsmanship that helped transform a tragedy into a new beginning.
Restoration Relief
Project: Ephrata Apartments
Location: Pennsylvania
On August 9, 2023, a devastating fire consumed all 12 units of an apartment complex at in Ephrata, PA. Despite the scale of destruction and logistical hurdles, the project team completed a full restoration in under 10 months, passing occupancy inspection on June 3, 2024.
One of the largest full-service projects undertaken by the company, the restoration effort was marked by tight scheduling coordination, clear communication across subcontractors and internal teams, and consistent updates to an out-of-state property owner in California. The team maintained 24/7 availability for displaced tenants, assisted with content recovery, and secured the site from unauthorized access, including addressing issues with squatters.
Several long-term cost-saving upgrades were implemented within budget, including replacing mixed flooring with durable LVP throughout and installing newer, low-maintenance systems. This project stands out not only for its technical execution and community responsiveness but also for the speed and scale of its delivery—restoring 12 full apartments on a busy main street in under six months.
SERVPRO Team Gutierrez
Project: Clarksburg Condominiums
Location: Clarksburg, Maryland
In August 2024, a devastating fire tore through Clarksburg Condominiums I, severely impacting 24 residential units, 20 storage closets, 10 garages, and multiple common hallways. SERVPRO Team Gutierrez led the emergency response and full-scale restoration of the complex, transforming a dangerous and destabilized structure into a safe, habitable living space within just 84 days.
This ambitious restoration effort demanded more than 7,000 labor hours from a 45-person crew, along with thousands of safety and mitigation supplies. Coordination with local officials—including code enforcement, county inspectors, and the Housing Opportunities Commission—was critical to the project’s success.
The team faced immediate hazards such as high CO2 levels, structural instability, and widespread flooding. A 24-hour safety hold from the fire department further complicated the start of work. With the building’s roof and structural integrity compromised, SERVPRO deployed a rapid-response plan that included securing the site, providing fire watch support, and facilitating resident property retrieval in coordination with the Red Cross.
Key innovations included engineering a temporary roof and shoring system to stabilize the structure and allow work to proceed safely. Advanced drying strategies—such as large-scale desiccant dehumidification—were also implemented to mitigate water damage and mold risk.
SERVPRO Team Gutierrez demonstrated leadership, technical expertise, and community commitment in delivering a complex, high-stakes restoration ahead of schedule—setting a strong example of excellence in the restoration industry.
Steamatic LLC, a Johns Lyng Group Company
Project: The Flood House – Disaster Restoration Training Facility
Location: Fort Worth, Texas
Steamatic LLC, a member of the Johns Lyng Group family, has redefined restoration training through the development of The Flood House—a groundbreaking facility designed to replicate real-world disaster conditions in a fully controlled environment. This state-of-the-art training center directly addresses one of the industry’s long-standing challenges: bridging the gap between classroom learning and high-stakes fieldwork.
Standard training methods often fail to prepare technicians for the unpredictability and intensity of real-life disasters. The Flood House closes this gap by offering hands-on education within a structurally realistic setting, simulating water, fire, and mold damage scenarios. It allows restoration professionals to practice and refine technical skills under pressure, ensuring greater accuracy, safety, and speed when responding to actual emergencies.
The facility is more than a training site—it is a symbol of Steamatic’s commitment to industry advancement. By investing in immersive, skill-based learning, Steamatic is empowering current and future professionals to raise the bar in restoration quality and response. The innovations demonstrated through The Flood House represent a major step forward in workforce development, customer satisfaction, and overall industry excellence.
Steamatic’s Flood House stands as a transformative contribution to the field and a strong contender for the Phoenix Award for Innovation in Restoration and Reconstruction.