Test Concrete for Moisture With Greater Ease
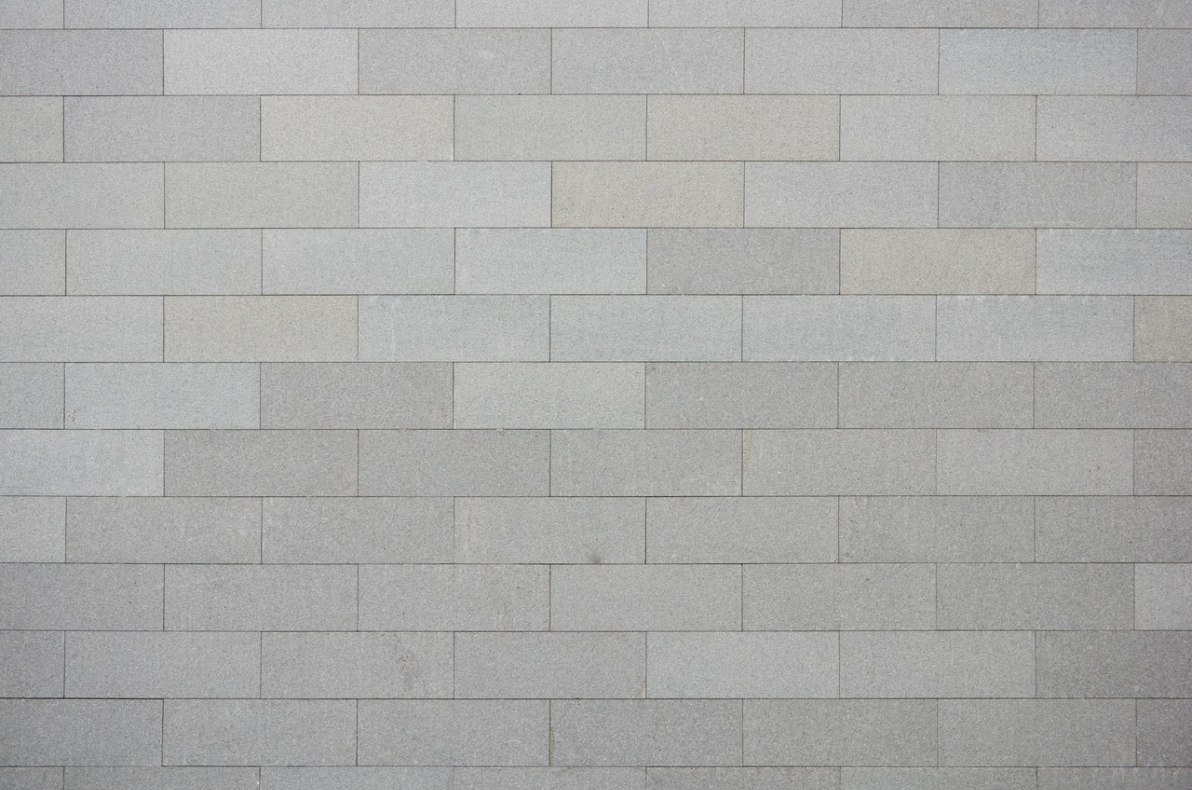
Even if a concrete slab has cured, it is never completely free of moisture. The porous nature of concrete allows moisture below the concrete and within it to migrate up through the concrete capillaries and escape through the path of least resistance, a process known as moisture vapor transmission (MVT). Excessive MVT can cause bonding failures or flooring to delaminate. Highly alkaline liquids can condensate underneath; cracking or bubbling of a floor covering or resinous floor coating system can occur; development of uneven walking surfaces can emerge, creating slip-and-fall hazards; the lifespan of the flooring material can be reduced; aesthetics can be damaged; floor covering warranties can be invalidated depending on the MVT limits; eventual deterioration of flooring and crumbling of the concrete substrate can occur; and mold or pathogen growth can develop either on top of the concrete slab or beneath the flooring material.[1]
Kelvin Rynhart, managing director of Tramex Moisture Meters, says technology has improved moisture meters, and with remote moisture monitoring of concrete, restoration technicians can save time and money. He says that in the 40 years that Tramex has manufactured moisture meters for the building and restoration industries, the industry has grown and works smarter than it ever has “with a greater knowledge of building material science.”
Restoration professionals must carefully measure moisture levels in concrete to ensure it is within allowable limits under ASTM F2170. The standard formally recognizes the use of in-situ probes as a means of conducting relative humidity (RH) testing. To do this, technicians must measure moisture vapor in terms of concrete RH or in terms of the rate at which the vapor is moving through the concrete.
For example, recent updates to the ASTM F2170 in-situ moisture test standard for concrete have made the once complex task of testing concrete for moisture easier and less time consuming. Companies had previously relied on the anhydrous calcium chloride test for concrete moisture vapor emissions rate, which is the rate of water vapor emissions from the surface of concrete and is determined with the use of a desiccant material sealed to the slab surface for a specified time period, then measured. Now, in-situ concrete moisture testing allows technicians to place sensors or probes inside the slab itself. As concrete dries, moisture migrates from the bottom of the slab to the surface, where it can evaporate away.
One of the biggest changes to the standard was the reduction in the time required — from 72 hours to 24 hours — to allow the test area to come to equilibrium before inserting the RH probe to take the measurement. “The change is mainly due to upgraded technologies used in modern RH probes,” Rynhart says. He adds that data loggers and remote monitoring can further assist restorers in reporting on moisture testing and the moisture conditions of various building materials.
One of the main benefits of ASTM F2170 in-situ monitoring is the ease of reporting. Data loggers enable the restorer to produce a report on site while automatically registering the location, time and date, as well as the ambient site conditions, which are called for in the standard but often overlooked, says Rynhart.
The benefits of remote monitoring of drying environments are many, including reducing necessary site visits. This can save hours of driving when job sites are at great distances, he adds. Alerts also can be set up to signal a failure in the system and whether machines are ineffective and need to be repositioned. Rynhart says, “These technologies were developed to make the drying technicians’ lives easier by creating savings among the two scarcest resources: time and money.”
[1] https://www.buildings.com/news/industry-news/articleid/21943/title/signs-concrete-floor-moisture