Go with the (Air) Flow
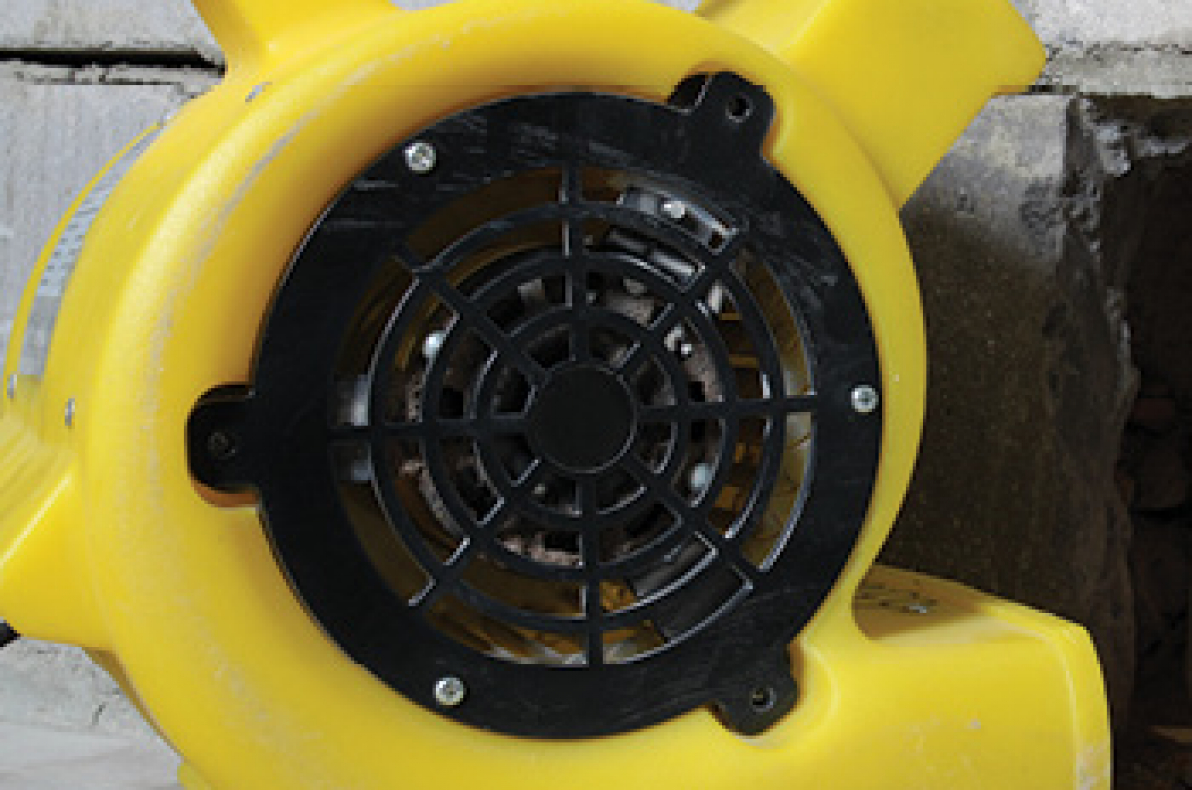
It is the trilogy of restorative drying — the holy grail: Humidity, air flow and temperature (collectively known as HAT). (Some add time as fourth element, but we consider time more of a byproduct rather than a critical factor, although the drying cycle (time) can be shortened by managing vapor pressure differentials.)
We are taught, even in a fundamentals class, that air flow is most important in the beginning of the drying process to necessitate evaporation of the boundary layer of moisture on hygroscopic surfaces. As a drying job progresses over time — assuming a balanced drying system was constructed at the onset — air flow will become less important, and dehumidification will become more important.
Setting aside dehumidification and temperature for a moment, what about air flow is so important? How much air flow is required? How should that air flow be administered? And lastly, at what point on the drying curve does air flow, at least high velocity air flow, become a barrier to drying rather than an aid?
Most practitioners place air movers in accordance with the S500, or use an iPhone app to suggest to them the number of air movers that should be placed. The S500 — even after the revisions that yielded the most recent edition 04 — is still weak on specifics regarding airflow. The acronym for cubic feet per minute (CFM) appears only three times in the entire S500 standard and guide, begging the question, “If airflow is so critical at the onset, why has there not been more guide data published in the standard and guide”?
The S500 still suggests air mover placement at between 10 to 16 feet intervals around the perimeter walls. But is that enough? And if a professional restoration contractor places more, in conflict with the standard, can it receive the remuneration for that variation from the standard? That, in fact, remains to be seen. But it would be nice to witness the effort firsthand. It would also be quite exciting to witness a contractor actually using an anemometer in the field to gauge the wind velocity being produced from the air movers, and how that air flow has contacted the surfaces.
The desired characteristics of air flow are that it needs to be laminar, free of turbulence, without vortices, and sustainable for a measurable linear footage beyond the initial source of the air flow. The distance from the wall and the angle of attack are determinate elements of air flow. Despite the fact that the S500 provides few specifics relating to air flow — almost relegating opinion on the subject to manufacturers of air movement equipment — there is some information available if an effort is made in discovery. In 2014, a white paper that speaks to the topic of air flow, “Air Mover Calculations in Structural Drying Projects,” was published by the IICRC S500 “Consensus Body.” The paper starts to define minimum air flow during the beginning of the drying curve — the constant rate of drying — and begins to view air flow within the definition of square footage of area to be dried. That suggested air flow is 600 FPM (plus) across all areas, floor or wall. The paper also substantiates other work published on the same subject.
One of the most important points or topics of discussion in both papers — one that is mirrored in our own in-house testing — is the air flow profile or dissipation of that air flow. The rate can be alarming. One of the key factors is the angle of attack to the wall. That angle can determine whether the air can remain laminar at measured intervals across the wall. Using a 2-foot grid, both away from the air mover across the wall and at 2-foot intervals up the wall, the air flow decrease is severe, as is the air flow rate dissipation.
Just two feet away from the air mover, the air volume drop, was critical (probably due to the distance from the wall and the angle of attack). The measured air flow two feet out and two feet up the wall was 25 percent of what it was at floor level, and at 2 feet out and 4 feet up, the air flow didn’t meet the threshold (100 to 250 FPM as defined in the whitepaper) for the falling rate part of the drying curve, let alone the minimum air flow for the initial start of the drying process, the constant drying rate part of the drying curve. Our model used a 12-block grid beginning 2 feet away from the air mover and ending at 8 feet and upwards from floor level, 2 feet and 4 feet up the wall. In only seven of those blocks did we reach minimum air floor (600 FPM) to begin the drying process.
As an industry, we don’t yet take the air flow rates as seriously as we should. We don’t yet apply the knowledge espoused within the referenced white paper, and we don’t measure air flow on the job site to determine whether we have adequate air flow at distances away from the air mover or up the wall that are conducive to drying. As practitioners, we may not yet have available to us products to assure the air flow needed. Placing air movers at 10 to 16 foot intervals just isn’t enough to still be able to call ourselves professionals.